Cathodic Protection Services
Normally used in conjunction with coating systems, cathodic protection is a dynamic preventative measure that can stop or reduce the rate of corrosion in aggressive soil or electrolyte conditions.
Electrochemical in nature, cathodic protection is used to prevent corrosion on buried or submerged metallic structures such as pipelines, storage tanks, and offshore structures.
Since 1950, Corrosion Service Company Limited has been at the forefront of advancing the science of cathodic protection and today ranks as one of North America’s leading specialist corrosion prevention companies. With highly trained engineers and technicians certified at various levels by the Association for Materials Protection and Performance (AMPP) and located across North America, Corrosion Service can design, supply, install, and maintain any type of cathodic protection system. Please select from the categories below, to learn how Corrosion Service is able to ensure the longevity of your assets.
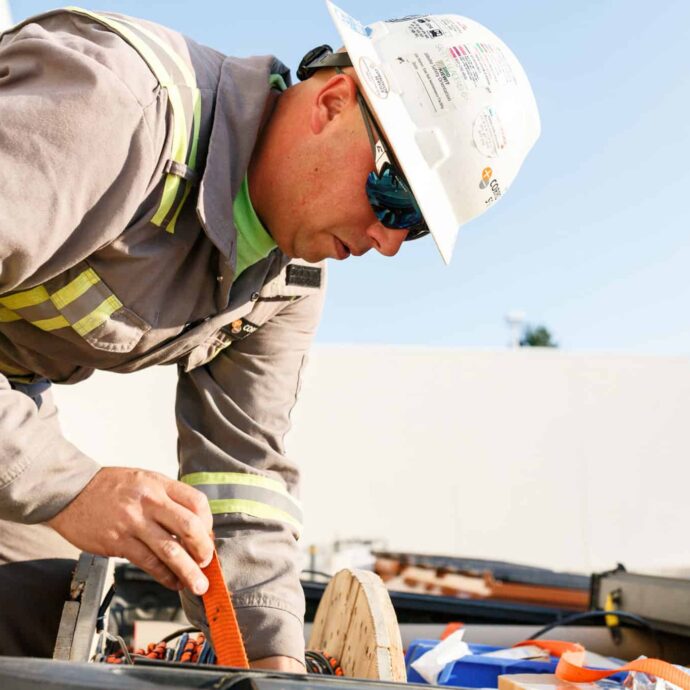
The Corrosion Service Technical Library that Documents our Past and Defines our Future
Since our founding Corrosion Service has been and remains a leader in the corrosion control industry, supporting the various industries in North America and around the World, ensuring asset integrity by providing responsible engineering services. As part of our continued commitment we would like to welcome you to our electronic Library as the place to view our various technical papers written and presented over the past 69+ years that have supported the corrosion industry advancement.
We also converted a prime corner office into a Library at our Head Office and dedicated the room to Sorin Segall for his commitment to Corrosion Service, the numerous papers he has presented, his engineering mentoring within Corrosion Service and our industry. We would be pleased for you to come and view this comprehensive library that includes various text books, relevant publications, all NACE Materials Performance magazines presented since first publication, technical bulletins and various other related corrosion related print material.
The History of Cathodic Protection
London 1824, cathodic protection papers were presented by Sir Humphry Davy to the Royal Society, and shortly after the first application of cathodic protection was to attach sacrificial anodes to the ship HMS Samarang. The anodes were made from iron and were attached directly to the hull clad copper sheath below the waterline. They were successful in dramatically reducing the corrosion rate of the copper. An unintended side effect caused additional marine growth on the copper hull and significantly reduced the speed of the ship. It was then decided to remove the anodes and let the copper corrode.
Michael Faraday was Davy’s assistant and continued his research following Davy’s death. In 1834, Faraday discovered the quantitative connection between corrosion weight loss and electric current and set the path for cathodic protection as we know it today.
Thomas Edison focused his efforts on impressed current cathodic protection for ships during 1890 and abandoned his efforts shortly after, as he could not find suitable rectifiers or anodes that could be mounted onto the ships’ hulls.
Around 1930 the oil and gas industry realized cathodic protection could reduce leak frequency and reduce the cost to maintain their assets and as they say, the rest is history.
Today cathodic protection is a critical component that protects our various industrial, commercial and consumer infrastructure assets.
Cathodic Protection System Types - Galvanic/Sacrificial Anode
Sacrificial anode systems are based on an electrochemically “active” metal (anode) attached to the asset metal surface (cathode) to be protected from corrosion when both are immersed in an electrolyte like soil or liquid.
Zinc, Magnesium or Aluminum metal alloys are commonly used as the anode, as these metal alloys have a native potential (more negative) than the cathode structure metal (i.e., the metal alloys are more electronegative). The asset metal is typically steel, but depending on the environment and corrosive nature of the electrolyte, the asset metal may be comprised of stainless steel, ductile iron, aluminum and or others.
Sacrificial anode systems do not require an external power source, are self-controlling and require very little maintenance. Their limiting factors is their ability to provide enough protective current for high current applications.
Cathodic Protection System Types - Impressed Current Systems (ICCP)
These systems consist of a direct current power source having an electrical cable connection to the structure to be cathodically protected and another cable connection to consumable anodes.
When AC power is available, the power source consists of a transformer rectifier. In the absence of an AC supply, alternative power sources such as solar panels, water wheels, wind power or gas-powered thermoelectric generators are commonly used.
Impressed current anodes are available in a variety of metallic alloys, shapes and sizes. Common anodes are tubular and solid rod shapes or continuous ribbons. The various anode materials, include high silicon cast iron, graphite, mixed metal oxide, platinum cladding and carbon steel.
Magnesium anodes or zinc anodes have been utilized for impressed current anodes but are rare and typically used in high resistance soil applications where the existing sacrificial anode systems were ineffective. A DC source is wired to the sacrificial anode to increase the driving force resulting in higher current outputs from the magnesium or zinc anodes.
For land-based assets like pipelines, watermains, etc, anode groundbeds can be horizontally distributed or installed in a deep vertical wells.
For water-based assets like docks, pilings, etc., the anodes are secured to the sea floor, suspended from pilings or secured to support structure.
Cathodic protection rectifiers vary from basic transformer diode rectification providing AC to DC conversion or custom offerings where the wave form is chopped providing high efficiency capabilities. A variety of additional features include remote monitoring, remote control, digital displays, integral GPS synchronous current interrupters, and various electrical enclosure types to house the components based on the environment to be located.
Cathodic Protection FAQ ( Frequently Asked Questions)
Cathodic protection is an electrochemical process that mitigates corrosion on pipelines, storage tanks, structural piles, and other buried or submerged metallic structures. Cathodic protection works by introducing a sacrificial metal that is electrically connected to another structure on which you wish to prevent corrosion. The anode is more anodic (more reactive) than the structure, and an electrochemical cell is formed where corrosion is significantly reduced on the structure, at the expense of corrosion on the anode.
Anodes are relatively inexpensive and can be replaced over time, so cathodic protection is used to significantly extend the operating lifespan of valuable pipelines, storage tanks, structural piles and other buried or submerged metallic structures.
Corrosion and cathodic protection are electrochemical processes. In a corrosion cell, the structure where metal loss (corrosion) occurs is always defined as the anode, and the structure that does not suffer from corrosion is defined as the cathode.
In cathodic protection, a sacrificial metal is introduced, connected directly to another more valuable structure on which you wish to prevent corrosion. The sacrificial metal is a more reactive metal and, subsequently, takes the brunt of the corrosion while preventing corrosion on the valuable structure. By virtue of its electrochemical nature, the anode forces the valuable structure to become the cathode, protecting it from corrosion, hence the term “cathodic protection.”
Corrosion prevention and control is a combination of technologies and techniques that mitigate corrosion risk on valuable steel infrastructure. This could include selection and application of coatings, cathodic protection, AC interference, DC stray current interference, and corrosion monitoring systems.
Cathodic protection is an electrochemical process. A sacrificial metal is introduced, connected directly to another piece on which you wish to prevent corrosion. The former is a more reactive metal and, subsequently, takes the brunt of the risk by converting active sites on the other metal’s surface to those of a passive nature, hence the term.
Cathodic protection systems offer an immediate and long-term solution to mitigate corrosion risk for buried and submerged steel structures. This translates directly to reduced maintenance requirements, lower operating costs, and improved asset longevity. It also makes operations more sustainable and environmentally friendly by utilizing fewer resources, since reducing corrosion through cathodic protection means that valuable infrastructure will last longer and need to be replaced less frequently.
Of course, another significant benefit is improved safe operation of assets, especially with high-visibility projects like pipelines, where failures due to external corrosion can be prevented before they even start, whether in corrosive soils/environments or at high-consequence areas, such as river crossings or urban areas.
Anodes are made from specific metal alloys that are more electrochemically active (“more anodic”) than the structure they are meant to protect. Examples of sacrificial anodes include magnesium, zinc, and aluminum. Examples of impressed current anodes are high silicon cast iron (HSCI) and mixed-metal oxide (MMO).
There are two commonly implemented means of cathodic protection. These formats are known as impressed current cathodic protection (ICCP) and sacrificial or galvanic cathodic protection.
Impressed current cathodic protection (ICCP) utilizes anodes with an external power supply source to provide the cathodic protection current. The external power source has a DC output, and can be powered by mains AC, solar panels, thermoelectric generators, or any other source of electricity.
ICCP systems are generally used where a large amount of cathodic protection current is required, such as for above-ground storage tank bottoms, complex piping facilities, long pipelines, or large offshore structures. ICCP systems are also used where soil conditions require a large driving voltage for cathodic protection current, such as in sandy or rocky soils.
Galvanic cathodic protection systems are powered by the natural electrochemical relationship between the anode (the more reactive metal) and the cathode (the protected structure, the more inert metal). Connecting the galvanic anode to the protected structure results in cathodic protection current flow simply based on the difference in electrochemical potential between the anode and cathode, requiring no external power source to drive the reaction.
Galvanic cathodic protection systems are used where a modest amount of cathodic protection current is required, such as for well-coated, shorter-length pipelines. You can often find these on steel or aluminum boats!
Cathodic protection is essential in preventing corrosion failures of valuable infrastructure. It is also a legislated requirement in most countries for the operation of oil and gas pipelines and storage tanks. the buildup of corrosion. Cathodic protection, combined with proper selection and application of coatings, provides a reliable method of mitigating corrosion risk and extending asset service life.
Anodes are made of a material that is more electrochemically active than the metal they are connected to. This is an intrinsic or natural consequence of what type of material they are, with gold being extremely unreactive, or more electropositive, but zinc or magnesium being much more reactive, or electronegative.
Anodes work simply by connecting them to a structure that is more electropositive than the anode material. The anode is always the most electronegative of all metals that are connected together, and corrosion occurs at the anode rather than at the cathode. In fact, in an unprotected steel structure, corrosion occurs at portions of the steel that act more anodic (more electronegative) than other portions of the same piece of steel!
When applying cathodic protection to steel, we select an anode that is more electronegative than steel, such as zinc, aluminum, or magnesium. If we are using an impressed current cathodic protection system, we can choose other anodes that may be more electronegative or electropositive than the steel, and we drive current out of them using an external power source.
Galvanization is the process of plating zinc onto a steel. From an electrochemical perspective, the zinc does provide cathodic protection to the steel if it ever becomes buried, submerged, or even just wet from rain or dew. So the zinc acts like an anode to mitigate corrosion on the steel, until the zinc is fully consumed.
The difference between cathodic protection and galvanization is that galvanization is applied to a structure at the factory and is not replaceable, and is only commonly available to certain materials (such as sheet metal, fence posts, or fasteners). Cathodic protection is field-installed, and can be used on any buried or submerged metallic structure.
When the galvanization is gone, it won’t come back, and the structure loses its corrosion mitigation and will start to corrode. When a cathodic protection anode is consumed, it is simply replaced, and the structure continues to have its corrosion mitigated.
Cathodic protection is useful for any infrastructure that requires corrosion mitigation to extend its service life, or to meet a minimum designed service life. Cathodic protection is usually implemented in larger, more expensive projects, or for projects where the structure being built requires a long (10+ years) service life. This can include pipelines, steel storage tanks, structural piles, and bridges.
Don’t worry. Our team at Corrosion Service is happy to assist. We fully understand that newcomers to these solutions may have a hard time deciding on which is best for their specific applications. Get in touch with us today if you require any further clarification or assistance.
Since our founding in 1950, we have built an extensive portfolio of specialist products for the corrosion prevention industry.
Our materials supply team has access to a full-range of Cathodic Protection materials both manufactured in-house and sourced from partner suppliers. Our dedicated supply chain team is based in Toronto alongside our material distribution hub, which is capable of delivering materials throughout the world on short notice.