Anotection® Anodic protection
Acid storage tanks, Piping & Acid Coolers
Contact Us
Anotection® - maximising acid purity by minimising iron contamination
Tank storage of Sulfuric Acid provides a critical link between production and consumption. But due to the corrosive nature of the acid, storage in carbon or stainless steel tanks will often result in hydrogen grooving, general corrosion and subsequent iron contamination. In order to maintain acid purity, Corrosion Service focuses on providing anodic protection design, engineering, supply and field services to Sulfuric Acid producers and consumers throughout the globe.
Anotection® is a proven technology developed by Corrosion Service in the early 1960’s. The electrochemical Anotection® system forms a protective film on the tank surface which is maintained by an electrical current. Anotection® is significantly more cost effective than linings, coatings and high alloys with well-maintained systems lasting in excess of 30 years.
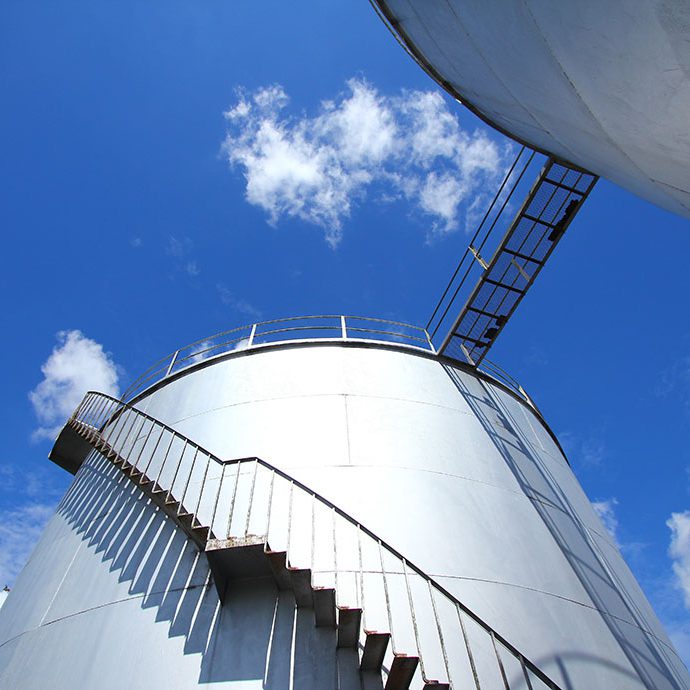
What is Anodic Protection?
Anodic protection is a means of preventing corrosion of metal in low pH (acidic) environments, usually sulfuric acid inside steel storage tanks or process piping. The anodic protection system creates a passive barrier on the steel’s surface that resists corrosion and prevents the release of corrosion products into the acid, and this helps maintain acid purity.
By installing an Anotection® system, your team can reliably protect your acid storage tanks and process piping from internal corrosion, reducing operating costs of maintaining acid purity as well as increasing tank and piping operating lifespan, reliability, and safety. Operators should seriously consider anodic protection solutions like Anotection® for applications in highly corrosive environments, where other methods such as coating or cathodic protection are less effective and more expensive.
Our team and the services that we offer
All Sulfuric Acid tank systems are different, and whether the project is new build, rehabilitation or routine maintenance, our talented team of industry professionals is empowered to understand the unique characteristics of every enquiry. This is important because as an organization, Corrosion Service strives to provide the extremely high level of support and partnership to provide the customized solutions that our clients require on a daily basis.
Anotection® is a proven anodic protection technology developed by Corrosion Service in the early 1960’s. The electrochemical Anotection® system forms a protective film on the tank surface which is maintained by an electrical current. Anotection® is significantly more cost effective than linings, coatings and high alloys with well-maintained systems lasting in excess of 30 years.
Our Process Engineering Group (PEG) is strategically located in Toronto, Canada and is the primary line of contact for Sulfuric Acid tank storage clients. PEG is designed to provide front line engineering expertise, project management support and field services in collaboration with our Toronto engineering hub that provides high level engineering and design services. Team members are highly trained with all engineering staff certified at various levels by the National Association of Corrosion Engineers.
Services
Our Anotection® Anodic Protection Field Services include:
- Annual Shutdown Support
- Anotection® System Installation
- Remote Monitoring
- System Audits
- System Maintenance
System Profile Downloads
Please click on any of the below to receive an email allowing download capabilities for the below system profiles:
The Corrosion Service Technical Library that Documents our Past and Defines our Future
Since our founding Corrosion Service has and remains a leader in the corrosion control industry, supporting the various industries in North America and around the World, ensuring asset integrity by providing responsible engineering services. As part of our continued commitment we would like to welcome you to our electronic Library as the place to view our various technical Anodic Protection papers written and presented over the past 69+ years that have supported the corrosion industry advancement.
We also converted a prime corner office into a Library at our Head Office and dedicated the room to Sorin Segall for his commitment to Corrosion Service, the numerous papers presented, the engineering mentoring within Corrosion Service and to our industry. We would be pleased for you to come and view this comprehensive library that includes various text books, relevant publications, all NACE Materials Performance magazines presented since first publication, technical bulletins and various other related corrosion related print material.
Anodic Protection History and Basic Principles
Designing, supplying and maintaining Anodic protection systems has been a core part of our business since the 1960s. These systems are primarily used for corrosion prevention inside green liquor tanks, Kamyr digesters, sulfuric acid storage tanks, heat exchangers and piping. Anodic protection theory is very similar to cathodic protection, the key difference being the structure is the anode. The negative terminal from the rectifier is connected to a submerged cathode made from highly corrosion resistant specialty rod or tube material. The greatest advantage of utilizing an anodic protection system is it allows the site to minimize their capital costs by constructing the vessel from commonly available mild or low-carbon steel.
Our anodic protection touch panel transformer-rectifier units (TPRU) or simply rectifiers are provided in standard ratings. They provide basic transformer diode rectification, AC to DC conversion, automatic system control, and can be modified to increase power efficiency in cases where the wave form is chopped. A variety of additional features are also available, including remote and local plant monitoring, remote control, digital displays, and suitable electrical enclosures for housing the components based on the environmental conditions.
Another major difference between anodic and cathodic protection is the higher output current required for achieving the required protection levels. Our systems range form 50-2000 amps of current capacity depending on the size of the structure, operating temperatures, and corrosivity of the product. The system works by maintaining the structure with enough current such that a thin stable passive film is formed on its surface. It is absolutely critical to maintain the reference potential in the passivation zone. Too little current and the structure will not be protected but too much current and corrosion is reintroduced at a rapid rate due to oxygen evolution.
Even with the high corrosive nature in this environment downtime is minimized and most systems are remotely monitored to ensure operating parameters are within the protective ranges otherwise an alarm is generated, and the client is immediately notified. An annual system audit is highly recommended to ensure the units continue to operate effectively in between shutdowns and minimize risk of corrosion. As well, during each shutdown we perform an inspection inside the vessels to verify the internal components are structurally sound and provide technical guidance with replacement work if necessary.
Anodic Protection Polarization Curve Through the Active to Passive Zone as Current Is Applied
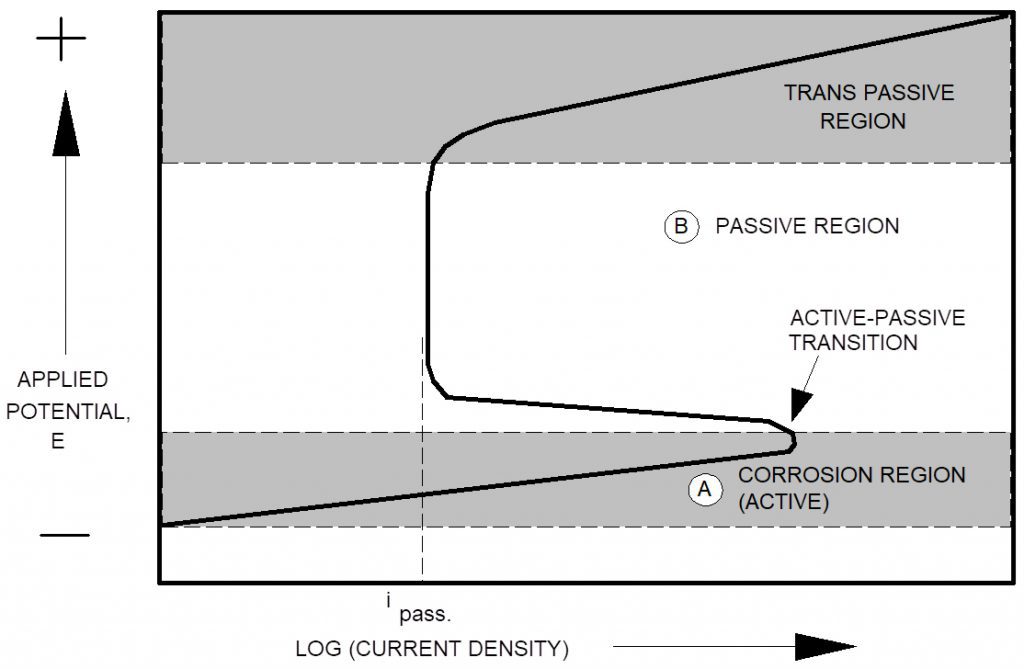
Since our founding in 1950, we have built an extensive portfolio of specialist products for the corrosion prevention industry.
Our materials supply team has access to a full-range of Anodic Protection mitigation materials both manufactured in-house and sourced from partner suppliers. Our dedicated supply chain team is based in Toronto alongside our material distribution hub, which is capable of delivering materials throughout the world on short notice.
Anotection Anodic Protection FAQ (Frequently Asked Questions)
Anodic protection is a corrosion mitigation strategy used for steel that is exposed to specific low-pH (acidic) environments, usually sulfuric acid inside steel storage tanks or process piping. The anodic protection system causes an electrochemical reaction on the steel surface to produce a passive oxide layer that mitigates corrosion. In anodic protection, we force the structure being protected to be the anode, and another device to be the cathode, so it’s the exact opposite of cathodic protection! Note that we only use anode protection in specific situations, and it is not interchangeable with cathodic protection.
Under low-pH conditions, anodic protection is used to electrochemically grow a passivating layer on the steel surface, such as the internal surface of a sulfuric acid storage tank. A monitored DC current source is connected to one or more cathodes and to the steel tank. The flow of DC current from the steel tank into the acid solution builds up the passivating layer on the steel surface.
Any corrosion of a sulfuric acid vessel will release impurities into the acid, such as iron sulphate, and also forms hydrogen gas. These impurities affect the quality and value of the sulfuric acid, as they affect the efficiency of the downstream process that uses the sulfuric acid. Sulfuric acid vessel corrosion also results in an increased cost to maintaining the required acid purity, and the formation of hydrogen gas presents a possible explosion risk and requires venting.
Anodic protection systems provide a cost-effective way of mitigating tank wall corrosion in sulfuric acid tanks, reducing the cost of maintaining acid purity and increasing the service life of the acid tank.
For tank, acid coolers, and piping surfaces, Anotection® is a thoroughly tested and proven anodic solution, having been in use for over half a century. Sufficient anodic protection minimizes the presence of contaminants, thereby reducing the risk of corrosion while maintaining acid purity.
Anotection® is the original anodic protection solution, designed by Corrosion Service in the 1960s. Decades of development and operational experience has resulted in Anotection® being the most reliable anodic protection system available on the market. In fact, our Anotection® are frequently used to replace other malfunctioning anodic protection systems!
Coatings and other linings that form a barrier between the steel vessel and the sulfuric acid degrade over time, resulting in progressive corrosion of the steel. The lifetime cost of maintaining acid purity and replacing the coating far exceeds the upfront cost of an Anotection® system. Anotection® provides a reliable and easily maintainable method of mitigating acid vessel corrosion and ensuring acid purity.